MCG makes lots of products, so of course we have lots of stuff to store. We’ve always maintained a facility near Atlanta, Georgia, which handles shipments to distributors and stores. It’s a very big warehouse (we aren’t the only company that uses it), and the staff there does a great job. But the focus there is on big orders going to a small number of recipients—not small orders going to thousands of destinations. As the MCG Shop grew, alongside our Kickstarter fulfillment needs, it became apparent early on that we needed a different way of getting product directly to you, our MCG Shop and Kickstarter customers.
Tammie took on the job. But we’re a distributed company—we all work from our homes, with no central office. So for a couple of years Tammie fulfilled your orders and Kickstarter rewards (tens of thousands of them) from her garage. At first, MCG’s business took up half the two-car garage space, but it didn’t take long before the car was consigned to the driveway and the garage was completely taken over by MCG product. A storage space was rented, and then another. It was clear we were going to need a better solution, so Tammie began looking for it.
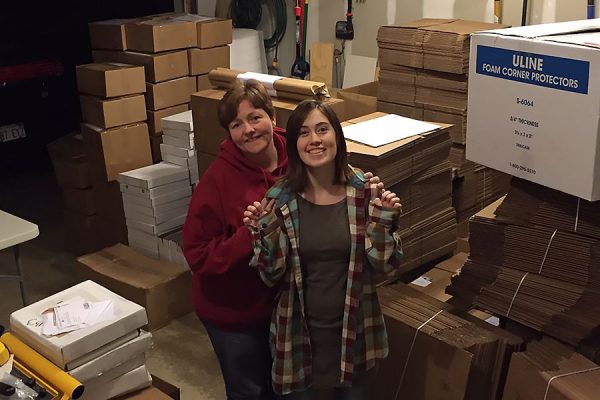
And she had great luck: A new facility was about to be built, exactly the size we needed and located very close to home and to the Post Office as well as UPS and FedEx offices. We signed a lease in January 2016. The original plan was to be moving in by May, but in the end construction wasn’t complete until August. (By that time, we were occupying six sizeable storage units as well as Tammie’s garage.) In the mean time, we watched the construction impatiently as the facility rose from an empty lot.
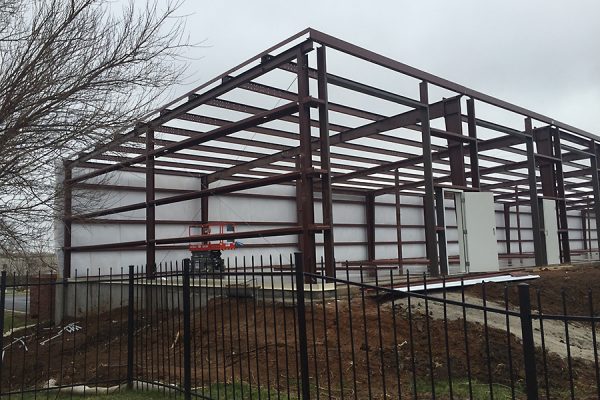
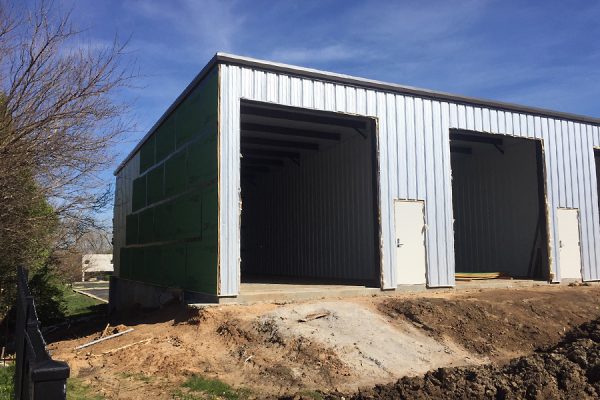
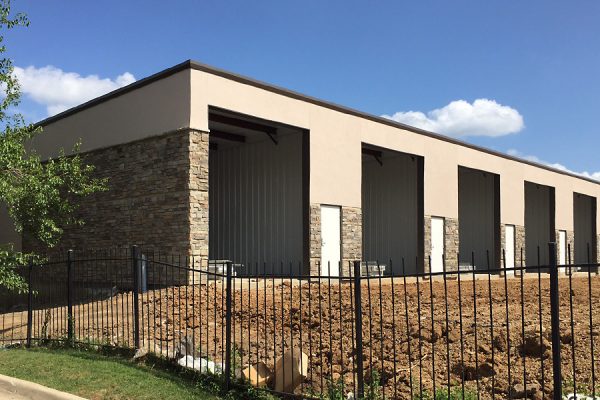
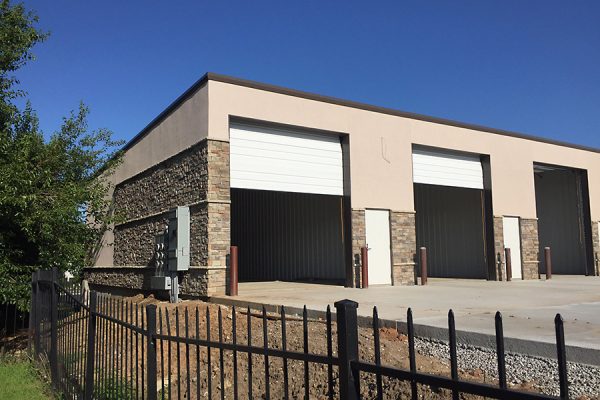
We did our initial move-in following Gen Con of last year, and began operations there in September. But the transition wasn’t immediately complete. It took a couple of months to get the climate control installed. (The winters here can get too cold to allow work in an unheated warehouse, and the summers can get brutally hot at times. And humidity control is important for keeping your books in good shape.) Over the months that followed we brought in more shelving and other infrastructure to make the packing process more efficient.
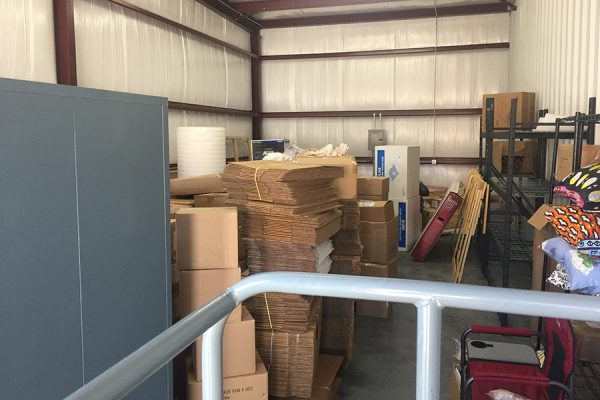
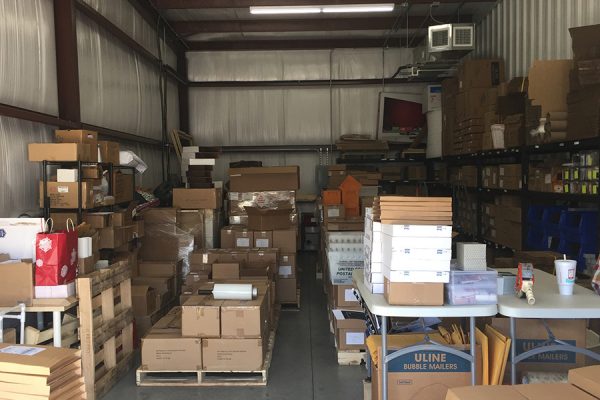
But we’re still growing, and soon even this huge improvement wasn’t enough. Once again we were running out of space. It was time to take the final step in our plan: Last month we installed pallet racking and bought a pallet stacker—sort of like a small forklift—to lift our 1500-pound pallets onto rack space as high as 12 feet above the floor.
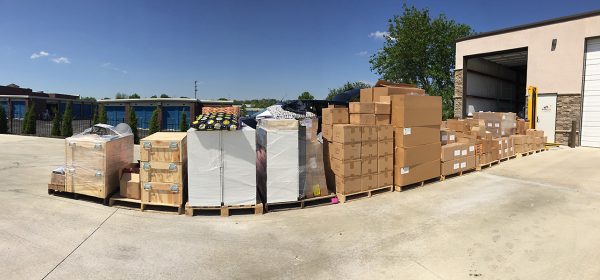
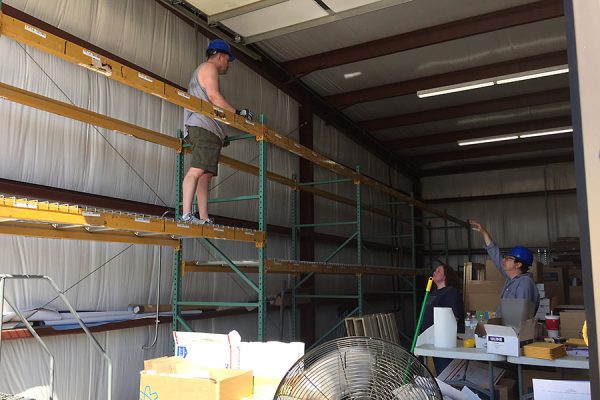
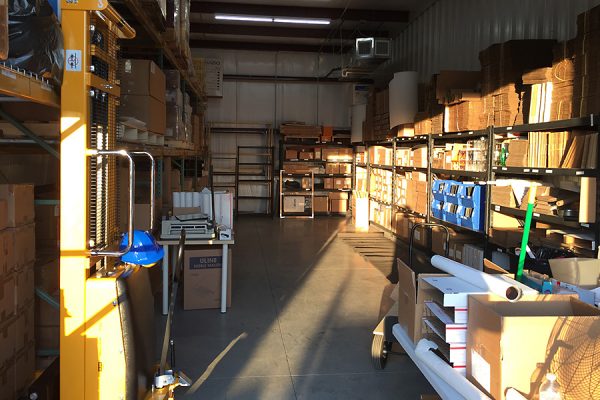
Tammie made all of these moves and adjustments without ever shutting down the MCG Shop or slowing our Kickstarter fulfillment. That slowed some of the move-in steps, but it was worth it.
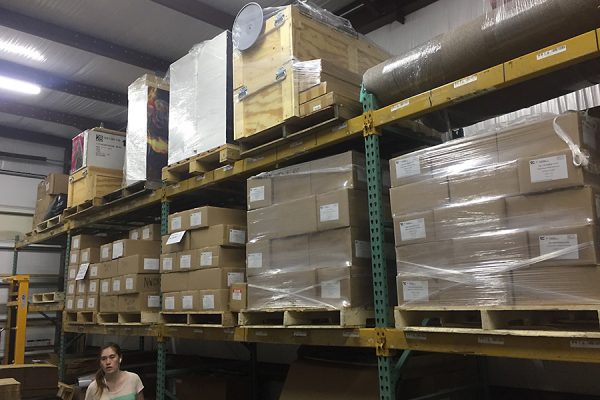
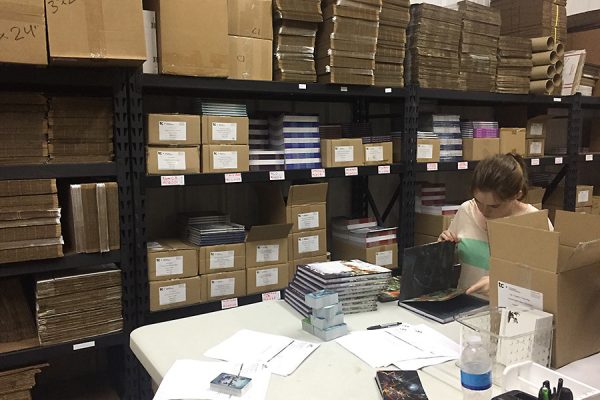